lookforjoe
True Classic
Fair enough, well fingers crossed neither of us will have to put into practice either theory. Hopefully that isn't because neither of them see the road again either.
Indeed!
Worked on the inner front fender barriers yesterday, and the grille insert. I opted to make the insert for install after the fenders are bonded, otherwise I have too many surfaces to bond simultaneously. Going to use 1/16" (.0625) 6061-0 aluminum sheet, rather than thinner steel sheet.
(front) forward sections
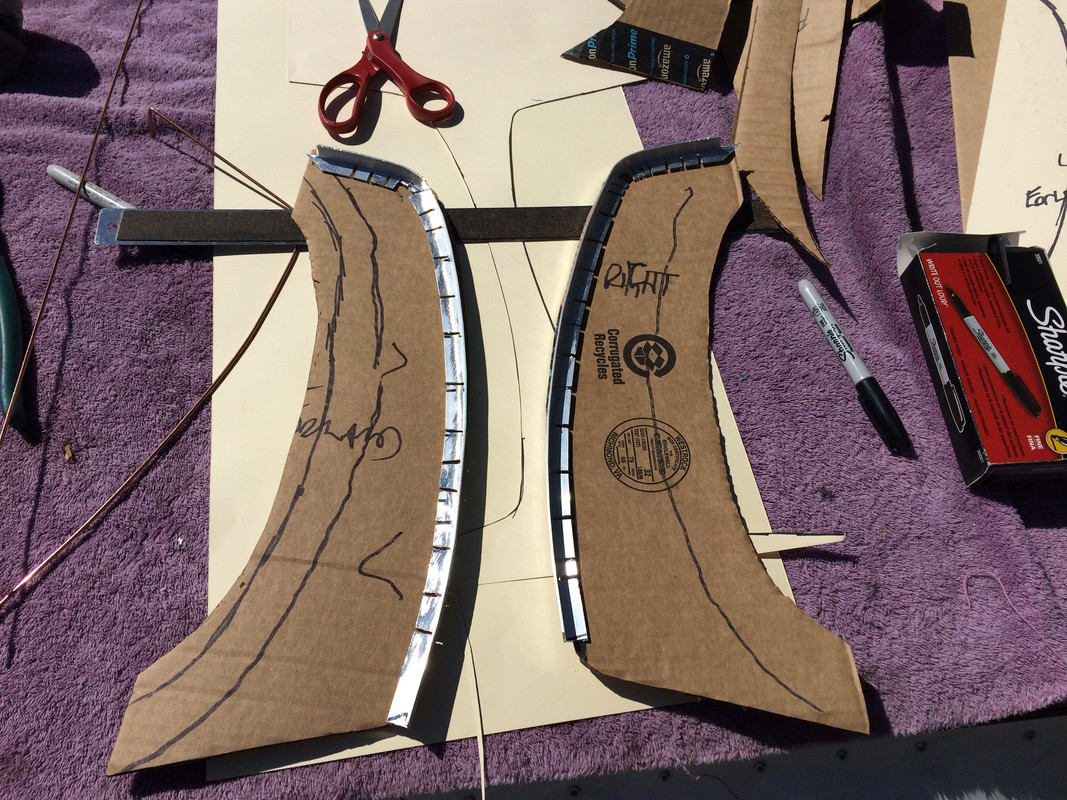
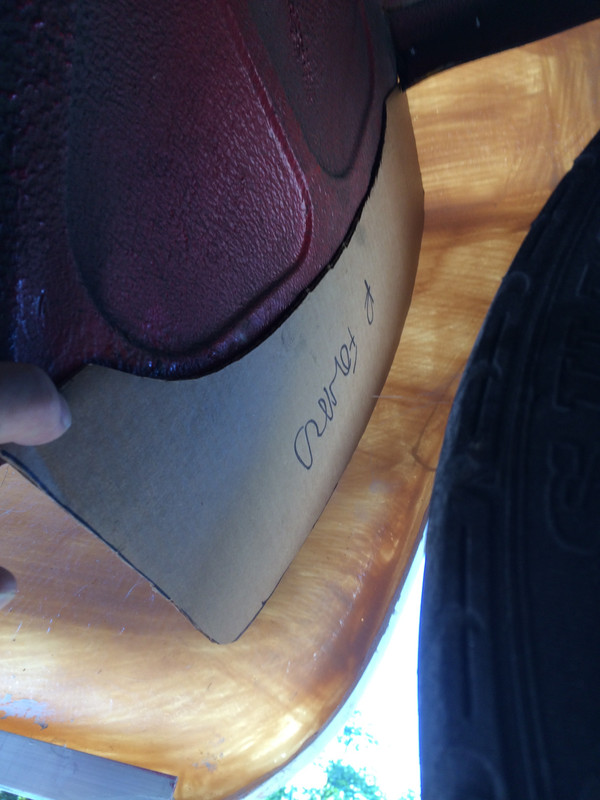
lip bonded to fender, flat insert will be bonded in place after nose is bonded. Been using Fusor 116 up to now, medium drying time. It is NLA, so I'm using 208b after this tube is done, it's a slower drying bond, which will be better for allowing time to position the entire nose panel and fender junctions.
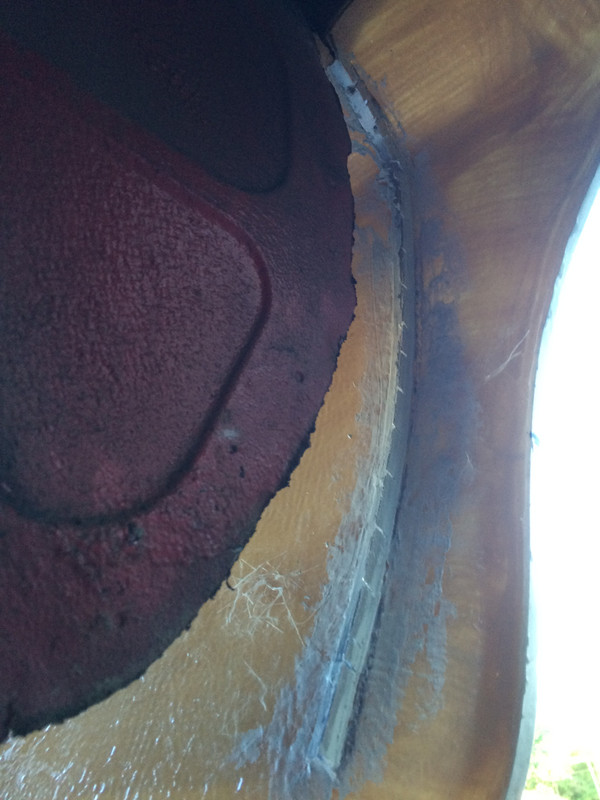
Inner (front) rearward template
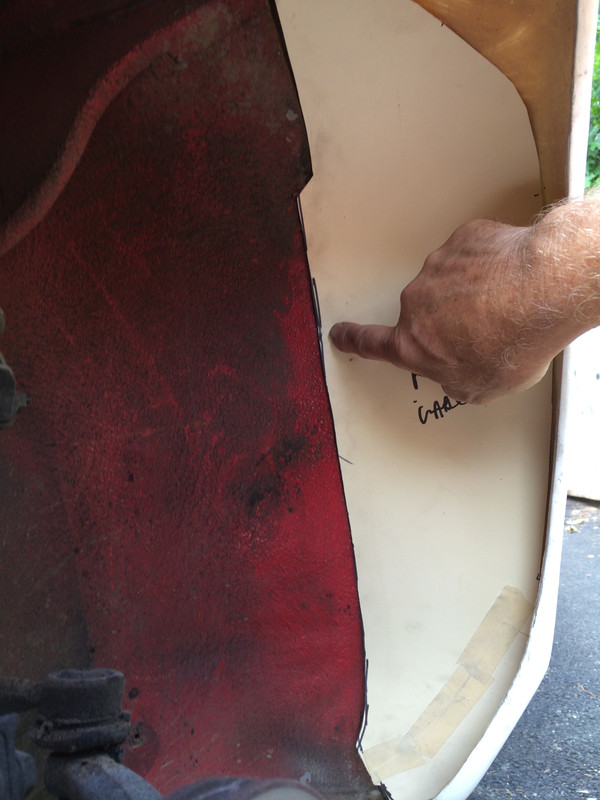
Found this grille mesh on eBay, closest I could come to to the original. Enough left over to make grilles for the side air intakes also, if I choose.
YT-600105 40 x 120cm
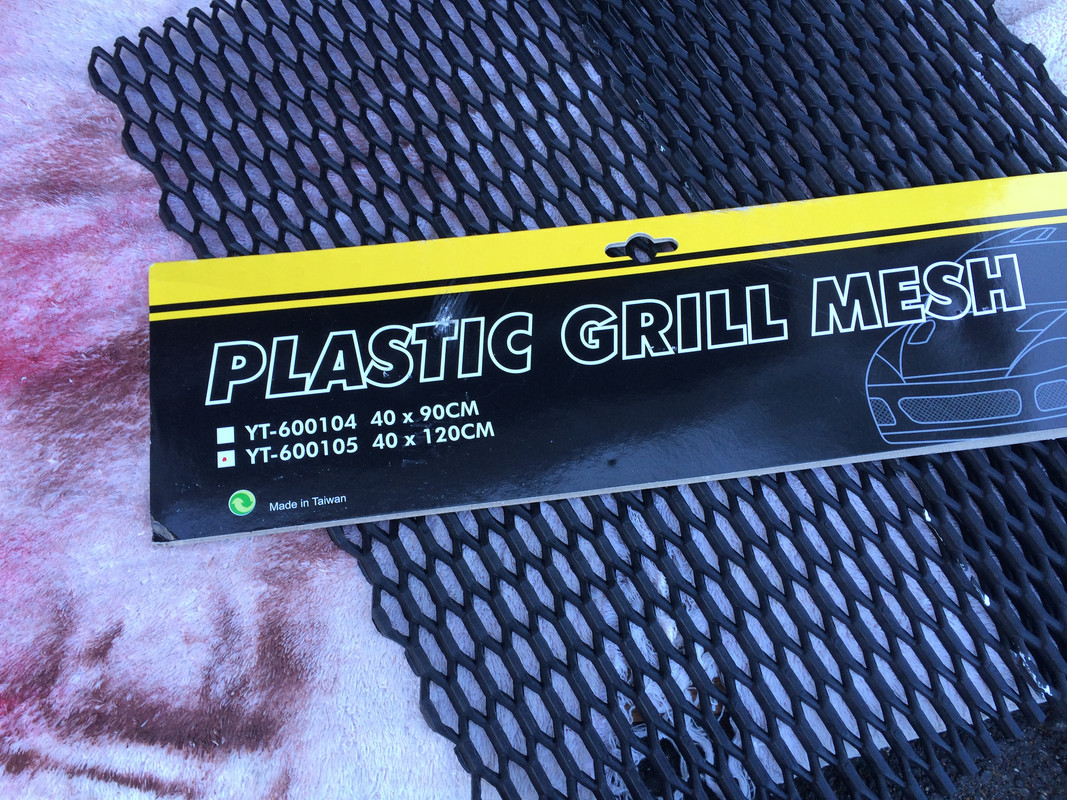
pics lightened to show mesh detail - going to remove / fill that licence plate recess area - don't want it & I'd never hang a licence plate in front of the air intake anyway.
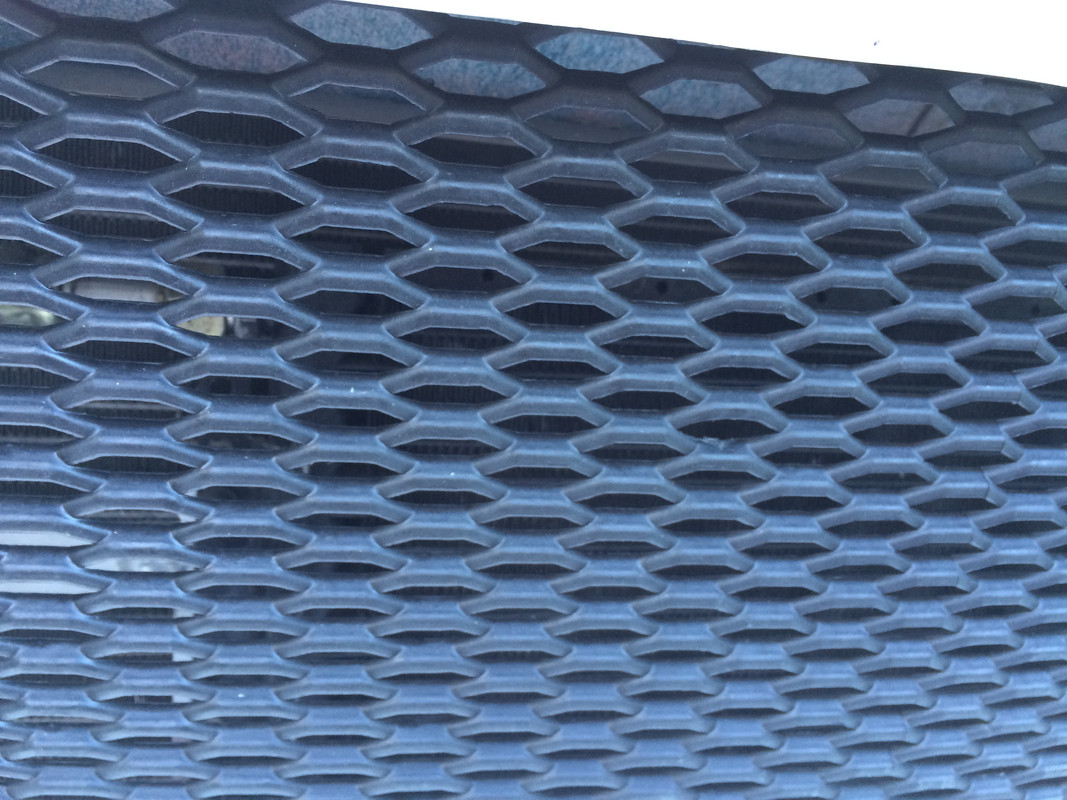
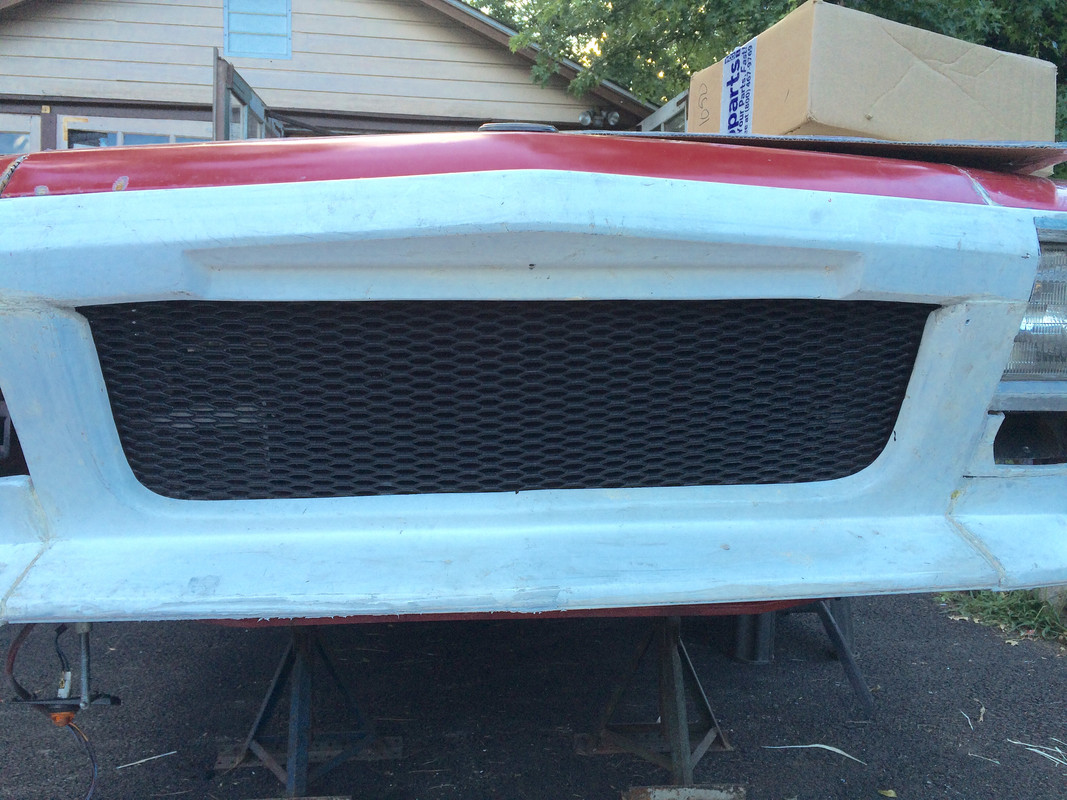
stock grille honeycomb
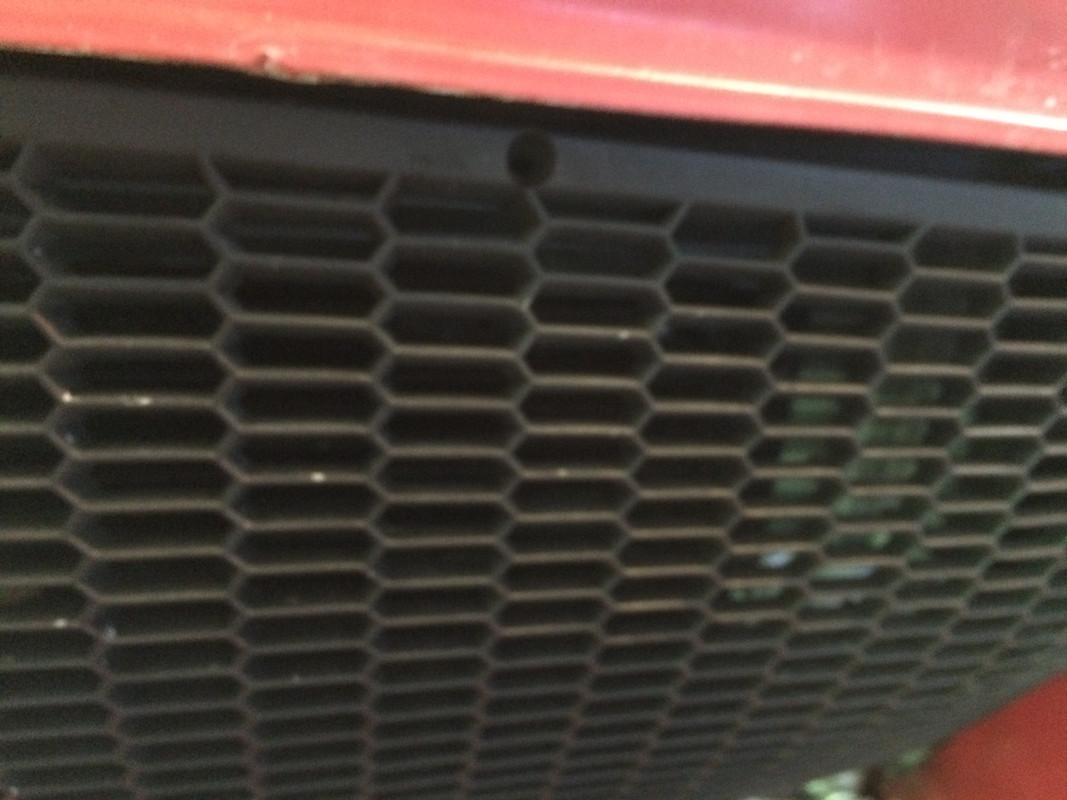
Sits in a trough, top & bottom. Material is flexible enough to push into upper trough, then flex & insert into lower trough. This way it can be removed & dropped down & out for access to AC fittings, etc. Have to trim & finish upper trough, and add side retainers to prevent lateral movement of the grille.
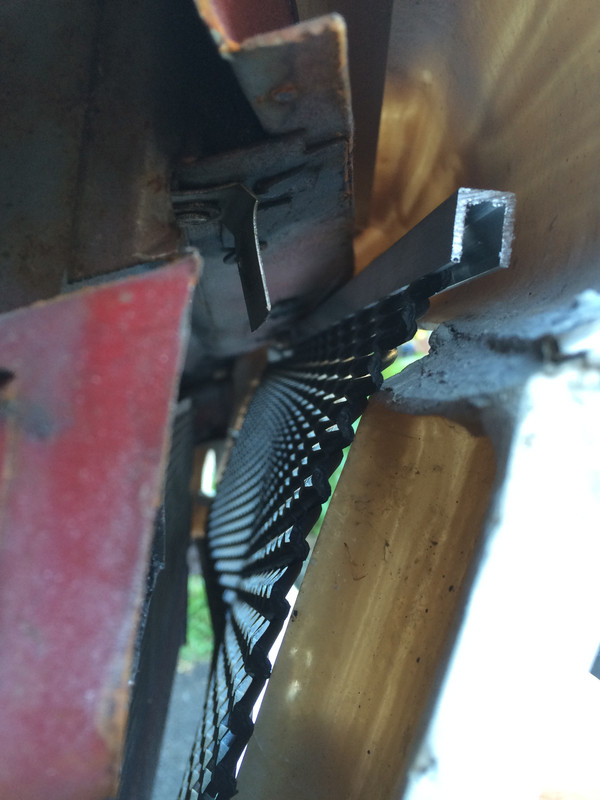
trough is set to 'tension' the grille material - forcing it to sit against the contour of the spoiler, otherwise it wants to lay flat, which would leave a gap along the bottom where grille meets spoiler, vs. the essentially flat upper contour.
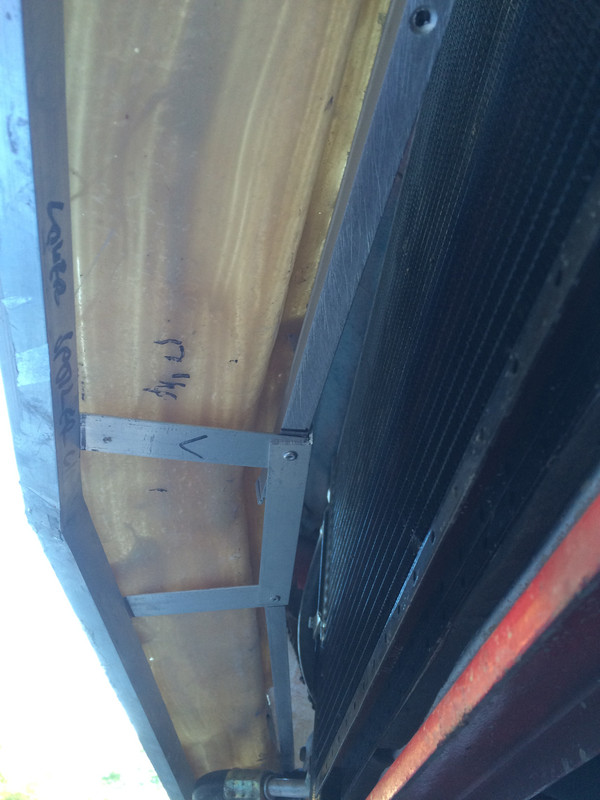
Last edited: